パレート図とは、全体の中で何の原因や事象が大きな影響を占めているかを明確にする為の手法です。
第24回~第30回のQC検定3級では以下のように出題されます。
試験(QC検定3級) | 第24回 | 第25回 | 第26回 | 第27回 | 第28回 | 第30回 |
パレート図 | 1問 | 1問 | 1問 | 1問 | 1問 | 1問 |
パレート図は第24回~第30回のQC検定3級では100%の確率で出題されています。
出題頻度が高いにも関わらず、難しい計算問題もなく比較的点数が取り易いので、しっかり覚えておきましょう。
出題傾向
QC検定3級では以下の3点について問われる傾向があります。
- パレート図についての基本的な説明
- データ表(補助表)
- パレート図の選択
1. パレート図についての基本的な説明
パレート図の基本的な事については、高い確率で問われます。
具体的には、以下の内容について覚えておきましょう。
パレート図の目的
冒頭で説明した通り、パレート図とは、全体の中で何の原因や事象が大きな影響を占めているかを明確にする為の手法です。
何の影響が大きいか明確にすることで、改善する事象を絞り込む事ができ、人的資源・時間・費用などを集中して効率的に改善する事ができます。
大きい事象を取り上げて改善する考え方を重点指向と言います。
パレート図の形
パレート図は不具合項目や作業項目などを層別したものを横軸にし、不良数、作業時間、金額(不良の損金失額)などを縦軸にします。
横軸は大きい順に並べ、棒グラフで表示します。次に横軸の項目を累積和でプロットして折れ線グラフで表示します。
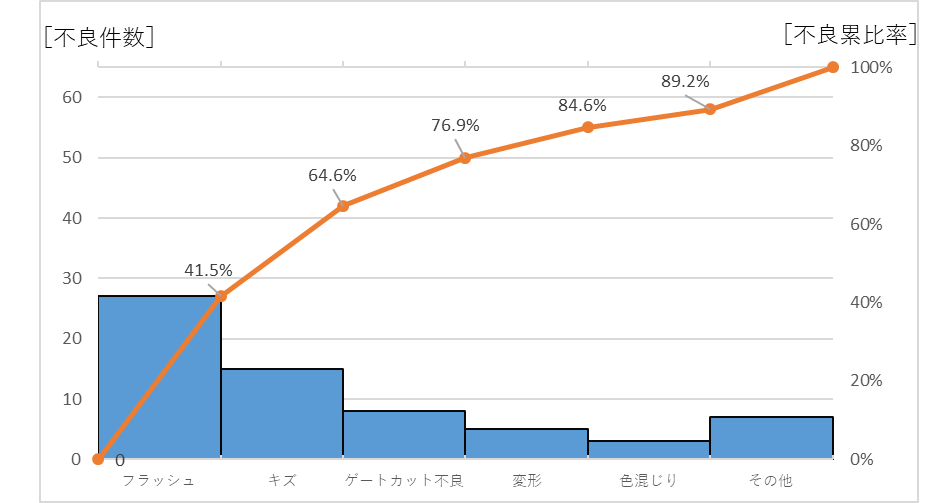
上図は、樹脂射出成形の工程内不良をイメージして作ったパレート図です。
棒グラフは不良件数、折れ線グラフは不良件数の累積比率[%]です。
棒グラフで各事象の大きさを確認し、折れ線で各項目までの全体の比率を確認する事ができます。
折れ線グラフで全体の比率を確認する事ができるので、何を優先的に改善すればいいのか視覚的に理解する事ができます。
例えば70%以上工程内不良を改善したい場合、フラッシュ、キズ、ゲートカット不良で76.9%を占めているので、優先的に改善を進めます(重点指向)。
3~4項目選択しても目標の割合(例えば70%)に到達しない場合は、項目の観点を変え層別し直す事が有効です。
2. データ表(補助表)
QC検定3級では高い頻度でデータ表(補助表)が出題されます。
出題される内容は以下の通りです。
- データ表(補助表)の作成
- ○番目に度数が高い項目を解答する
- 件数 ⇒ 損失金額や損失時間に変換する
問題自体は簡単なので、本番は落ち着いて解きましょう。
データ表(補助表)の作成
下図のように度数がバラバラのデータ表から、度数の大きい順に並べたデータ表を作成しします。
QC検定3級では、作成後のデータ表の穴埋め問題などが出題されます。
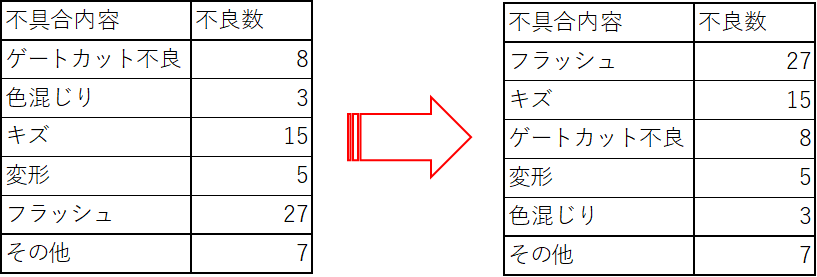
次に、度数の大きい順に並べたデータ表に累積和や累積比率を追加します。
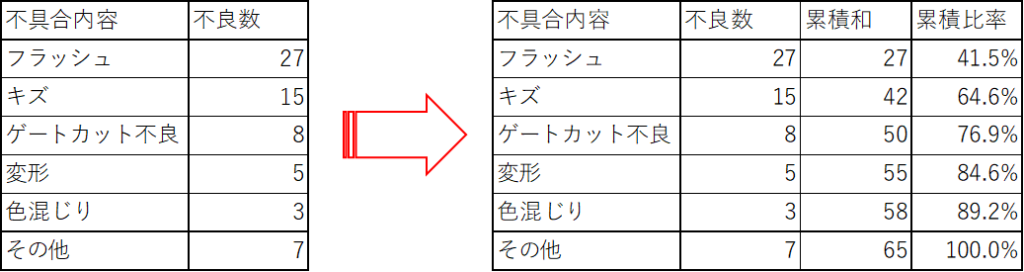
累積和は度数の高い順に足し合して算出します。
例えば「キズ」までの累積和はフラッシュ+キズで42(27+15)になり、「変形」までの累積和はフラッシュ+キズ+ゲートカット不良+変形で55(27+15+8+5)になります。
○番目に度数が高い項目を解答する
こちらはデータ表から、1番目または2番目に度数が高い項目を選択します。
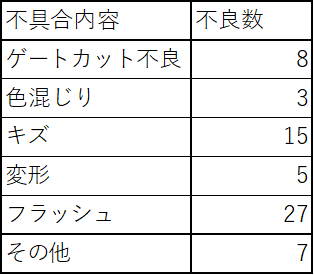
例えば上表で1番目に高い項目は「フラッシュ」、2番目に高い項目は「キズ」になります。
件数 ⇒ 損失金額や損失時間に変換する
データ表を度数の大きい順に並べた後、項目を「件数」から「損失金額、またほ損失時間」に変換する事を求められる事もあります。
具体的には不具合などの件数と、その1件当たりに掛かる損失金額や時間を掛けて、その項目トータル損失金額や損失した時間を算出します。
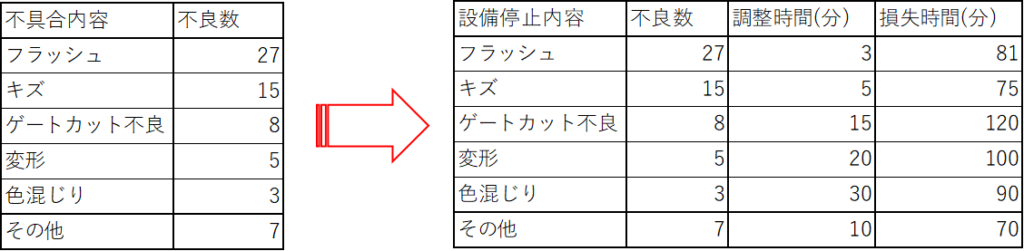
上表を例にすると、「不良数」×「調整時間」で「損失時間」を算出します。
「損失時間」を算出した後は、損失時間の大きい順に並び変え、パレート図を作成します。
パレート図の選択
第24回~第30回で2回パレート図を選択する問題が出題されました。
これはデータ表の値などのは関係無く、パレート図の基本的な作成方法や形状を覚えていたら簡単に解答する事ができます。
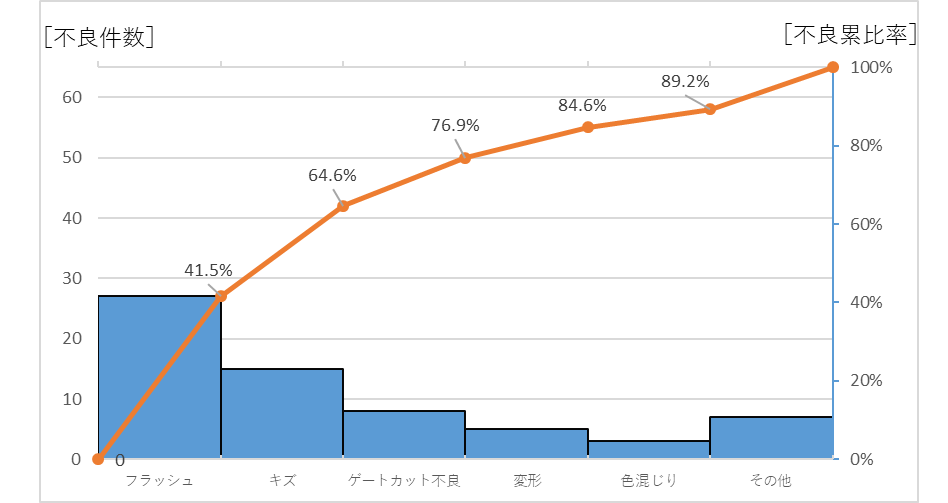
具体的には以下の事を覚えていれば、正解のパレート図を選択できると思います。
- 棒グラフは左から大きい順に並ぶ(その他は除く)
- 棒グラフの最後はその他
- 折れ線は0からスタートし、最終的に100%になる
- 折れ線は最初が大きく上昇し、順番に上昇度合が小さくなる(その他は除く)
下記に参考としてパレート図の作成方法も記載しておりますので、良ければご覧ください。
【補足】パレート図の作成方法
パレート図を作成する時は以下の手順で行います。
QC検定3級ではここまで問われない箇所もありますが、パレート図の理解を深めるのに必要と思いましたので、参考に記載させて貰います。
①使用目的を明確にする
何の為に調査するかで項目が変わるので、目的は明確にする必要があります。
例えば、設備停止を要因を横軸に作成する場合、目的によっては縦軸が設備停止の件数、設備停止時間、設備停止よるコストなど、内容が変わります。
②データ収集・整理
目的を明確にした後に横軸になる分類項目を決め、データを収集します。
データ数は少なければ誤差で事実とは違うパレート図・見解になる可能性があるので、1週間、1カ月とある程度まとまったデータが必要です。
また収集したデータは、パレート図にする前に表でまとめます。
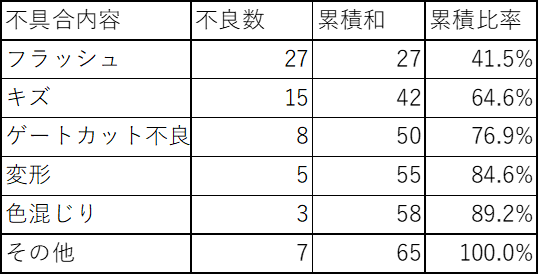
表でまとめる際に以下の注意が必要です。
・データを大きい順に並べる
・データの小さい物は「その他」でまとめる
・「その他」はデータの大きさに関わらず、最後にする。
・データの隣に累積和を作成
※累積和・・・データを累積した値 上表を例にすると、27、27+15、27+15+7・・・とデータを順番に足していく
・累積和の隣に累積比率を作成
累積比率・・・累積和 / 総和(上表だと65)
③パレート図の作成後、見易く整える
作成した表からパレート図を作成します。
パレート図を作成する際は以下の事を行い、見易く整えます。
・棒グラフの各項目間の隙間を無くす。
(棒グラフを太くする)
・折れ線グラフの始点を(0,0)にする
Excelだと第2横軸の軸オプション(書式設定)の軸位置を目盛にチェックすると始点を(0,0)にできます。
・棒グラフの右角と折れ線グラフの1点目を合わせる
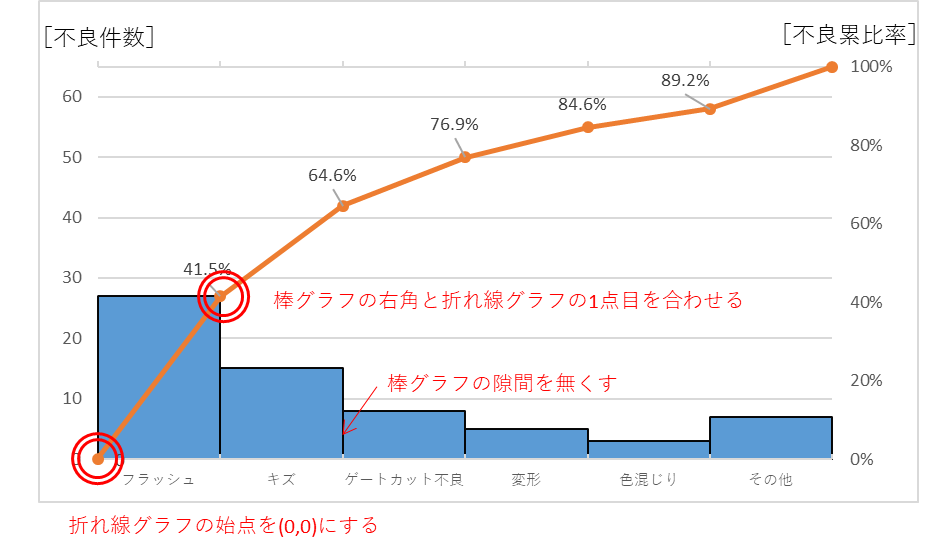
④完成したパレート図で解析・検討する
完成したパレート図で各項目の大きさと、全体の比率を確認します。次に影響が高い順番に、どこまで改善するか決めます。
例えば改善の対象を70%にする場合は、下表のように「フラッシュ」「キズ」「ゲートカット不良」の改善を行います。
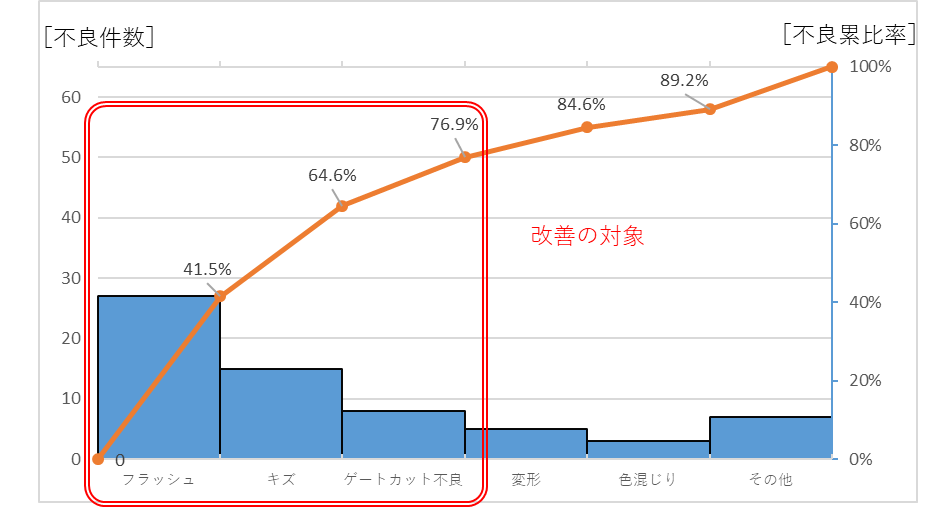
コメント